Pick-and-place robots are a critical part of modern manufacturing and automation. Their ability to identify pick, and position objects with speed and accuracy determines overall performance. However, these systems face challenges in environments with inconsistent lighting and rapid movements. The See3CAM_37CUGM based on the Sony® IMX900 global shutter sensor and powered by e-con’s Proprietary TintE ISP introduces advanced imaging capabilities to solve these issues.
This global shutter USB camera, introduced by e-con Systems, is the first of its kind to feature built-in HDR support. With Quad HDR functionality, it processes RAW sensor data through the high performance TintE ISP, ensuring high-quality imaging even in dynamic environments. A simple USB connection enables direct integration into robotic systems, making it a powerful solution for pick-and-place applications.
In this blog, you’ll learn how e-con Systems’ Sony IMX900-based See3CAM_37CUGM easily addresses the challenges of pick-and-place robotics while adding immense value.
How See3CAM_37CUGM Solves Challenges Faced by Pick-and-Place Robots
Challenge: Mixed lighting and motion distortion
Pick-and-place robots operate in environments where lighting conditions are far from uniform. Shadows cast by robotic arms, bright reflections from metallic surfaces, and transitions between artificial and natural light sources create inconsistencies in object visibility. Standard cameras struggle to maintain clarity in these conditions, often producing underexposed or overexposed images.
Also, when moving at high speeds, traditional cameras with rolling shutters introduce distortions, leading to inaccurate object positioning. Misalignment in visual data can cause placement errors, disrupting production workflows.
Solution
e-con Systems’ See3CAM_37CUGM uses Quad HDR technology to record varying light intensities within a single frame. The camera enhances object detection across various lighting conditions by balancing contrast dynamically. So, the objects remain visible in both shadowed and brightly lit regions, eliminating exposure inconsistencies.
For reflective metal surfaces and shiny plastic covers, Quad HDR plays a major role in minimizing glare and preserving contrast. When scanning barcodes or serial numbers, reflections from these surfaces can cause standard cameras to either overexpose the bright areas or lose details in darker regions.
Quad HDR counteracts this by capturing multiple exposure levels and merging them into a single well-balanced image, preventing washed-out highlights and retaining clarity in text and patterns. The camera’s ability to reduce light saturation also ensures that high-contrast details, such as barcode lines and engraved serial numbers, remain sharp and readable. Hence, pick-and-place robots can accurately process information on reflective components without errors.
Furthermore, See3CAM_37CUGM’s global shutter sensor captures the entire frame simultaneously, eliminating motion-related distortions.
Challenge: Inconsistent detection of small or fast-moving parts
Pick-and-place systems frequently handle small components, such as microchips, electronic connectors, and delicate mechanical parts. Inconsistent lighting conditions can cause these objects to appear washed out or too dark, reducing detection accuracy. Moreover, when robotic arms move between different lighting zones (from a shaded area to bright light), standard cameras will struggle to adjust exposure levels quickly enough. This delay in adaptation can result in misreads or failed picks.
Solution
e-con Systems’ See3CAM_37CUGM comes with a fast auto-exposure feature, enabling it to adapt quickly to changes in brightness. Hence, even when robotic arms move between light and shadow, this camera maintains clarity without requiring manual adjustments. Rapid exposure control is crucial in high-speed production lines, where even slight delays in imaging can impact system performance. Thereby, ensuring stable exposure levels and eliminating fluctuations in brightness is how See3CAM_37CUGM enhances detection accuracy for small and fast-moving parts.
Other Key Features of e-con Systems’ See3CAM_37CUGM for Pick-and-Place Robots
Quad HDR function
e-con Systems’ See3CAM_37CUGM harnesses a Quad HDR function, which processes RAW sensor data through e-con’s TintE ISP, optimizing image quality even in environments with extreme brightness variations. This is because traditional cameras often struggle to capture clear images in scenarios where bright highlights and deep shadows exist within the same frame.
See3CAM_37CUGM captures multiple exposures at different intensity levels and merges them into a single frame, ensuring a well-balanced image with clear details across the entire lighting range. Its FPGA-based processing also reduces the computational burden on external processing units. So, the robotic system can allocate more resources to decision-making and motion control, resulting in a faster, more responsive system with minimal latency.
Self-trigger mechanism
In many automated environments, external triggers are typically used to signal when an image should be captured. However, these external components introduce additional complexity, requiring additional hardware integration and calibration. e-con Systems’ See3CAM_37CUGM eliminates such dependencies with its self-trigger function, which enables automated image capture based on activity within predefined sensing regions.
So, instead of relying on external sensors to initiate image capture, the camera can autonomously detect when an object enters the scanning field and trigger a capture sequence, improving throughput while reducing system complexity.
Global shutter with higher FPS
e-con Systems’ See3CAM_37CUGM integrates global shutter technology, ensuring that all pixels in an image are exposed at the same time. Unlike rolling shutter cameras, which capture images line by line, global shutter sensors capture a full frame instantly, which eliminates distortion caused by rapid movement. When robotic arms move rapidly, a rolling shutter camera can create skewed or warped images, leading to misalignment during object placement.
However, the See3CAM_37CUGM, with its global shutter architecture, makes sure that every frame retains clear, undistorted object edges, even when tracking fast-moving parts.
See3CAM_37CUGM also comes with a high frame rate, reaching up to 850 fps with a custom region of interest (ROI). This makes it easy to adjust the ROI so that the robotic vision systems can focus processing power on key areas of the frame in real time.
So, pick-and-place robots that operate at high speeds can track objects with exceptional accuracy, thereby reducing the chances of missing fast-moving parts. Custom ROI functionality also helps in optimizing data transfer rates by capturing only relevant sections of the frame, reducing processing load and increasing real-time responsiveness.
e-con Systems’ See3CAM_37CUGM is a High-Performance Sony IMX900-Based Camera
Since 2003, e-con Systems has been designing, developing, and manufacturing OEM cameras. One of our latest products, See3CAM_37CUGM, is the first global shutter USB camera based on the Sony IMX900 sensor with built-in HDR support.
Use our Camera Selector to view our end-to-end portfolio.
If you need help integrating the best-fit camera into your robotic vision application, please write to camerasolutions@e-consystems.com.
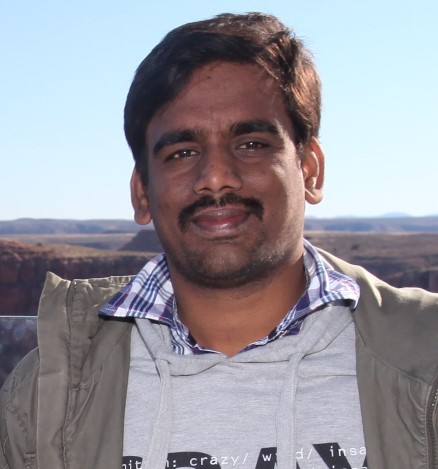
Suresh Madhu is the product marketing manager with 16+ years of experience in embedded product design, technical architecture, SOM product design, camera solutions, and product development. He has played an integral part in helping many customers build their products by integrating the right vision technology into them.