Pick and place robots play a crucial role across many industries, considering their ability to intelligently handle repetitive and labor-intensive tasks. They are generally used to pick up objects and place them in designated spots, operating across industries to achieve high throughput and streamlined workflows. Traditionally, pick and place robots depended on static programming, restricting their ability to adapt to changes in object orientation, size, or position.
Over the past few years, however, state-of-the-art camera solutions have helped these robots unlock a new level of imaging intelligence. It has equipped them to leverage real-time data to analyze and interpret their surroundings before changing their actions.
In this blog, you’ll get expert insights on the role of cameras in these robots, their main challenges, popular use cases, as well as measurable business benefits.
Camera-Related Challenges of Pick and Place Robots
Measurement errors
Even slight measurement errors in measuring an object’s dimensions can majorly affect a robot’s precision. Robotic arms can struggle to handle objects properly without clear imaging and accurate measurements. It potentially leads to operational errors, damaged goods, or workflow disruptions.
Difficulty in grasping
When robotic arms lack accurate dimensional data, they face difficulty securely grasping objects. It may be frequent while handling those with irregular shapes or varying sizes. So, without the right camera input, robots misjudge grip strength or positioning, resulting in failed handling attempts.
No depth perception
As you may know, a limitation of 2D camera setups is the absence of depth data. So, pick and place robots depend on 3D imaging to judge how far an object is from the lens or the robotic arm. However, many existing 3D imaging solutions still face challenges, leading to missed picks, awkward angles, or collisions during object handling when items are stacked or randomly oriented.
Inaccurate object dimensions
Robotic arms depend on camera input to calculate movement paths. If the imaging system fails to capture exact object dimensions, the robot’s movement becomes unreliable. Misjudged coordinates or shape data may cause weak grips or failed placements in high-speed environments.
Lack of human-like vision
Robotic arms require 3D vision to adapt like human hands. Standard imaging doesn’t help the robot understand contours, curves, or slight object shifts. Such a gap makes it tough to handle irregular or delicate items that need nuanced grip adjustments during motion.
Why Cameras are Integral to Pick and Place Robots
Package dimensioning
Pick and place robots need to measure object dimensions accurately to execute successful picks. With the help of cameras, they can analyze the size and volume of items without requiring manual input. This supports tasks like sorting or stacking, where object dimensions directly impact robotic movements.
Object detection
Cameras enable pick and place robots to locate and identify objects on the conveyor or workspace. The imaging system captures visual data to help the robot differentiate between various items, even when they vary in shape, material, or placement. It reduces dependence on human intervention so that robots can function autonomously.
Object orientation
Cameras also help assess the orientation, ensuring the robot can understand how the object is positioned. This is required for pick and place robots to grip items correctly, especially when objects are placed at odd angles or have rotated in transit. Therefore, with the right imaging setup, the robot can adjust its grip and alignment in real time.
Quality control
Integrated camera systems also support quality inspection. They compare live images to preset quality benchmarks to detect defects or inconsistencies and take corrective actions. This includes rejecting faulty items or flagging them for review, ensuring that only conforming products move forward in the workflow.
Automated safety
Cameras play a major role in maintaining safety on automated lines. They constantly monitor object flow and surroundings for the robot to detect anomalies or obstructions. The visual feedback minimizes the risk of collision, reduces downtime, and helps maintain a smooth and safe operation environment.
Types of Cameras Used in Pick and Place Robotics
The choice of camera depends on the complexity of the task, the need for depth perception, and the environmental conditions. Let’s look at some of the most widely used cameras:
2D cameras
Two-dimensional cameras capture flat images that show the x and y coordinates of objects. These cameras are ideal for applications where depth information is unnecessary. They are commonly used in basic sorting tasks, enabling robots to differentiate between objects based on size, shape, or color as long as the objects are positioned consistently on a flat plane.
For instance, in an electronics assembly line, 2D cameras can help identify circuit board components and guide the robot’s arm to place parts accurately.
3D cameras
3D cameras provide a three-dimensional perspective for embedded vision applications that require depth information. They enable robots to detect z-axis data, which allows them to understand the height and orientation of objects. Hence, in scenarios where items may be randomly stacked, this can be very critical.
The additional depth data enables pick and place robots to maneuver complex shapes, grasp objects at different heights, and adjust their orientation for accurate placement. For example, in logistics, items are often jumbled in containers. So, with 3D cameras, the robot can see and pick items without displacing others.
RGB-IR cameras
RGB-IR cameras combine standard color imaging (red, green, and blue) with infrared (IR) capabilities, ensuring a broader spectrum of vision across various lighting conditions. They capture visible and infrared wavelengths to enhance object recognition and accuracy in environments with inconsistent lighting.
For instance, in automotive part assembly, RGB-IR cameras help pick and place robots to perform quality inspections even under suboptimal lighting. Standard cameras may struggle to accurately capture these parts due to reflection. However, with IR capabilities, an RGB-IR camera can bypass the effects of visible light reflections and detect the true contours and alignment of each component.
Popular Vision-Based Use Cases of Pick and Place Robots
Manufacturing
Pick and place robots can identify, sort, and arrange components based on type, color, and size. Cameras provide the robots with real-time feedback, enabling them to pick and place objects in the correct orientation or sequence. They also play a major role in quality control by inspecting products for defects or irregularities, ensuring the robots can detect cracks, discoloration, incorrect alignments, etc.
Warehousing and logistics
Pick and place robots equipped with cameras manage inventory by scanning barcodes, identifying package dimensions, and sorting items based on order requirements. This reduces errors, accelerates speed, and ensures better organization in warehouses. Additionally, they can help track inventory in real time, providing data on item availability and locations. The result? It simplifies stock management and reduces misplaced items while enabling on-time restocking.
Electronics
Pick and place robots can help place small and delicate components, such as microchips, onto circuit boards with minimal error. With the right cameras, the robots can detect the exact positioning required for each component, handling even minute adjustments for accurate placement. Furthermore, they perform micro-assembly tasks by working with components on a very small scale.
Pharmaceuticals and medical devices
In the pharmaceutical industry, pick and place robots handle medications and medical devices within sterile environments. Cutting-edge cameras ensure the robots can help maintain cleanliness while assembling or sorting items, thereby reducing contamination risk. These robots can also inspect medical devices and pharmaceuticals to verify labeling, packaging integrity, and overall quality. It goes a long way to make sure that all products meet stringent standards before reaching the market.
How the Right Camera Can Benefit Pick and Place Robots
- Enhanced accuracy: Pick and place robots can easily identify and locate objects with heightened accuracy. This minimizes errors, which makes them perfect for high-stakes industries where accuracy is a make-or-break moment.
- Increased speed: Pick and place robots can boost the speed of operations by driving real-time decision-making. They can perform tasks without the need for constant reprogramming, which results in faster handling of several objects in one workflow.
- Improved flexibility: Pick and place robots can adjust to changing variables such as object shape, size, or orientation. It means they can handle a multitude of tasks, which makes them important in environments where production needs fluctuate.
- Higher quality assurance: Pick and place robots can support quality control by inspecting each item as it moves through the production line. Any discrepancies are immediately flagged, reducing the chances of defective products reaching customers.
Now that we’ve explored the benefits of using cameras in pick and place robots, how do you choose the right one for your application? Stay tuned for our upcoming blog, How to Select the Right Camera for Pick and Place Robots, where we’ll guide you through the key factors to consider when making the best choice.
e-con Systems Offers World-Class Cameras for Pick and Place Robots
Since 2003, e-con Systems has been designing, developing, and manufacturing OEM cameras. Over the years, we have helped clients successfully integrate world-class camera modules into their autonomous mobile robots, including pick and place applications. We deliver both custom and ready-to-use cameras that come with features such as HDR, LFM, synchronized multi-camera setups, global shutter technology, and more.
Explore our AMR vision expertise.
Check out our Camera Selector Page to see our complete product portfolio.
If you’re looking to integrate the best-fit cameras into your pick and place robots, please write to camerasolutions@e-consystems.com.
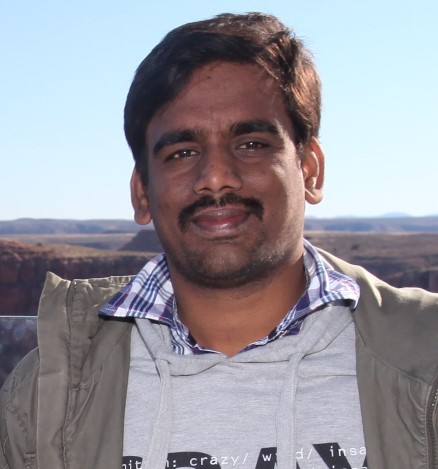
Suresh Madhu is the product marketing manager with 16+ years of experience in embedded product design, technical architecture, SOM product design, camera solutions, and product development. He has played an integral part in helping many customers build their products by integrating the right vision technology into them.