Automation is rapidly transforming production lines, and pick and place robots are an integral part of this shift. These robots help move objects from one location to another with speed and accuracy, which streamlines workflows in manufacturing, logistics, packaging, and other industries. For instance, they are used for sorting items in warehouses, assembling electronic components, and handling fragile goods in the food industry. It goes a long way to reduce human involvement in repetitive tasks, ultimately contributing to higher productivity, more operational safety, and consistent output quality.
As you can imagine, pick and place robots need the right cameras to guide their movements. Unlike conventional robotics applications, pick and place robots tend to be deployed in dynamic environments where high-quality visual data is required to make decisions on object location, orientation, and movement. Hence, choosing the right camera is a crucial factor.
In our previous post – What is the role of cameras in pick and place robots? – e-con Systems, we explored how cameras enhance precision and efficiency in pick and place robots. In this blog, you’ll discover how cameras operate in pick and place robots, as well as the key camera features that make it all possible.
How Cameras Work in Pick and Place Robots
Cameras in pick and place robots serve as the “eyes” of the system for the robot to identify, locate, and interact with objects. They process critical visual information so that the robot’s control system can make informed decisions about where to move objects and how to handle them.
Let’s take a closer look at how cameras work in pick and place robots:
- Object recognition: Cameras capture images of the target objects, which are then processed by vision algorithms to detect features such as shape, size, color, and texture. It helps distinguish the target item from its surroundings. For example, in a sorting application, the camera system can differentiate between items based on size or color. Therefore, the robot can make quick decisions on handling different objects.
- Positioning and alignment: Once the object is recognized, the robot needs accurate data on its position and orientation. Using 2D or 3D cameras, the system can evaluate the precise object coordinates, equipping the robot to adjust its movements accordingly.
- Quality control: The camera helps perform quality checks to identify defects or inconsistencies by comparing real-time images with predefined quality parameters. The robot can flag or remove defective items from the line, thus maintaining product quality standards.
- Speed of responsiveness: Since pick and place robots often operate at high speeds, the cameras used must deliver fast, real-time feedback. High frame rate cameras are preferred in these applications, as they allow the robot to make split-second adjustments to its movements, increasing throughput without compromising on accuracy.
Selection Criteria: Must-Have Camera Features of Pick and Place Robots
2D vs. 3D imaging
2D cameras are suitable for applications where objects are consistently positioned and do not require depth information. These cameras capture flat images, providing data on shape, color, and general features. They are often used in simpler pick and place tasks, such as sorting items of similar size and height.
On the other side, 3D cameras are necessary for depth perception-related tasks, which include picking randomly oriented objects or handling items stacked at various heights. These cameras use the structured light or time-of-flight approach to measure the distance between the camera and objects, providing spatial data for the robot to navigate complex arrangements.
High resolution
Only high-resolution cameras can produce the type of image detailing that enables robots to distinguish fine features and minor variations between objects. It also supports accurate identification of small components for pick and place robots that require handling, such as electronics assembly or quality control,
High Dynamic Range (HDR) + LED Flicker Mitigation (LFM)
HDR and LFM features are absolutely necessary for environments with varied lighting conditions. HDR enables the camera to handle scenes with both bright and dark areas, ensuring clear imaging without loss of data. LFM is crucial where LED lighting is used, as it prevents flickering in the captured image, which could otherwise disrupt object detection and classification.
Global shutter
In high-speed pick and place robots, global shutter cameras capture images without distortion, making them ideal for pick and place robots. Unlike rolling shutter cameras, which can distort fast-moving objects, the global shutter feature ensures crisp, undistorted images that support accurate positioning and movement tracking, particularly in environments where items move quickly on conveyor belts.
Multi-camera synchronization
Multi-camera synchronization is a must-have capability for tasks that demand a comprehensive view of an object. By aligning multiple cameras, the pick and place robot can capture images from different angles, which provides a 360-degree view for accurate object recognition and placement. It can be tremendously useful when objects have complex shapes or orientations that need to be fully understood for proper handling.
Inbuilt Image Signal Processor
An inbuilt Image Signal Processor (ISP) optimizes image quality directly on the camera, adjusting factors such as exposure, color balance, and noise reduction in real time. It reduces the processing load on the robot’s control system, driving faster decision-making. An ISP also enhances image data quality for pick and place robots, making object detection algorithms a lot more reliable.
IP69K-rated enclosure
Many pick and place robots operate in harsh or dusty environments. Thus, an IP69K-rated enclosure protects against water, dust, and extreme temperatures. It ensures the camera’s longevity and performance stability.
Software integration (for object detection)
Software integration should be seamless for the pick and place robot to effectively use object detection algorithms. It includes compatibility with platforms that support machine vision and deep learning, enabling real-time analysis and decision-making. Proper integration also ensures pick and place robots can execute tasks such as sorting, identifying specific components, and quality checking with greater accuracy.
e-con Systems’ Camera Solutions for Pick and Place Robots
e-con Systems has been designing, developing, and manufacturing OEM cameras since 2003. During this time, we have integrated several camera modules into autonomous mobile robots, including pick and place robots. We have worked with multiple customers to deliver custom and off-the-shelf cameras with features such as HDR, LFM, multi-camera synchronization, global shutter, and more.
Learn about our AMR imaging expertise.
Use our Camera Selector to see our full portfolio.
If you need any help in finding and integrating the right camera into your robotics applications, please write to camerasolutions@e-consystems.com.
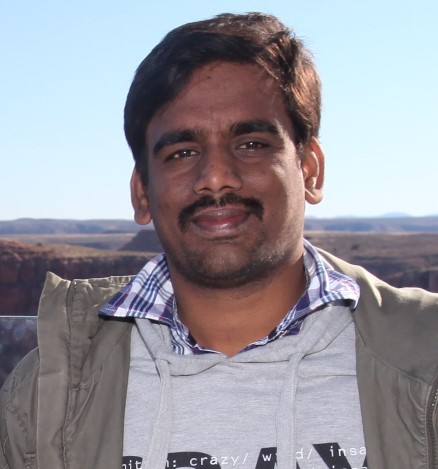
Suresh Madhu is the product marketing manager with 16+ years of experience in embedded product design, technical architecture, SOM product design, camera solutions, and product development. He has played an integral part in helping many customers build their products by integrating the right vision technology into them.